|
|
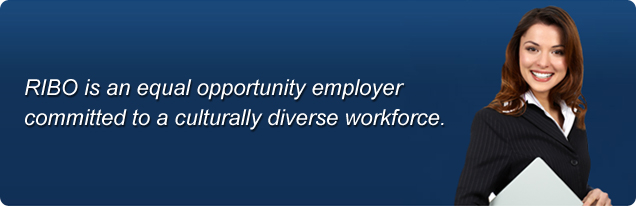 |
|
Description
Supervise a medium to large group of employees involved in 3-shift operational plant production facility. Work is generally of a technical nature with the ability to make decisions within the limits of general standards and practices.
- Responsible for the effective use of personnel, material, and equipment - Meets production cost schedule and maintains quality requirements - Complies with the terms of local and national labor agreements - Implements divisional and corporate policies - Implements safety and good housekeeping standards - Frequent contact with others outside the work group - Keeps management informed of developments as they occur - Maintains corporate and unit management control systems. - Maintains department records - Utilize statistical methods and data from voice of customer and voice of process for continuous improvement - Maintain awareness of quality standards, communicate department quality goals and leverage resources to solve quality problems - Drive first time quality in station - Build and maintain good working relationships with employees, union and management - Motivate, train and develop employees to effectively perform their jobs utilizing standardized methods - Assist in the training and development of salaried and hourly employees - Achieve production schedules and product requirements by applying lean manufacturing/synchronous principles with emphasis on variation reduction - Assist in the development of assembly/manufacturing processes for area of responsibility - Control costs and achieve productivity improvements - Provide input to payroll and perform other administrative tasks, as required
Qualifications
- Knowledge of manufacturing processes and procedure - Must be able to work a flexible and rotation schedule: 1st, 2nd or 3rd shift - Ability to manage a team - Experience supervising employees in a union and manufacturing environment - Team-oriented and operated - Knowledge of basic math - High level oral and written communication skills - Knowledge of basic technology of area where assigned - Knowledge of scheduling and other management systems - High level analytical ability where problems are complex - High level interpersonal skills to work effectively with all levels of the organization, motivate employees and elicit work output - Knowledge of quality control and safety procedures - Knowledge of GFit, which is a computer Quality System that retrieves data - General assembly experience at least one year - Demonstrated ability to effectively organize and plan - Demonstrated thorough knowledge of the total manufacturing process, including work process flow, plan and work station layout and tooling, related to area of responsibility - Demonstrated thorough knowledge of lean manufacturing/synchronous principles - Demonstrated thorough knowledge of computer and control systems applicable to area of responsibility - Demonstrated knowledge of financial management concepts to improve costs - Demonstrated thorough knowledge of tools, materials, equipment and processes for respective area of responsibility
Education and Training
- Minimum of 3 years of experience as first-line supervisor of hourly employees - Bachelors degree or equivalent training, plus additional training such as that acquired in the first one or two years of college or technical school - Completion of recommended Corporate training programs
» More Career Opportunities
| | | |
|
|
|
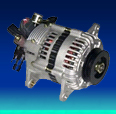 |
RB-ALT061 |
|
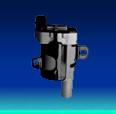 |
RB-IC5006 |
|
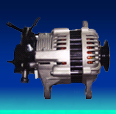 |
RB-ALT060 |
|
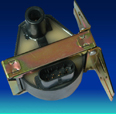 |
RB-IC2805A |
|